
CATALOG
Books
Brushes
Dyes
Resists
Supplies
Color Charts
Accessories
Moyer Design Fabric Stretching System
Order Form
CLASSES
Retreats
Workshops
Private Classes
Tips and Techniques
GALLERY
About Susan Moyer
Contact Us
LINKS
STUDIO SAFETY,
World Batik Conference 2005 and The Surface Design Conference KANSAS CITY 2007
HAWAII-07 Workshop Review & Photos
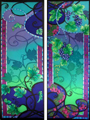
BANNER commission for Peidmont Community Church
Home
|
Stretching your silk on the Moyer Design Fabric Stretching System
New TIP
To accommodate additional length and width when assembling the Moyer Design(TM) Fabric Stretcher, arrange the stretcher bars so the loops, elastic and hooks run along the outside of the stretcher, then attach the legs. Attach the silk corners first and then center the silk. Once the silk is centered attach the middle of each side and proceed by attaching the rest of the hooks. If the silk is wrinkled or creased, remove the wrinkles by wetting the stretched silk with a clean sponge brush and water. Be sure the silk is dry before applying a resist or latex treatment.
New Tip
Woven silk has memory so it will return to its original shape after being removed from a fabric stretcher. Therefore, when painting symmetrical design elements, such as a vase or geometric design versus organic shapes, it becomes crucial to first stabilize the silk so that it can be squared up and stretch evenly. Otherwise, the painted image may appear wobbly once it is removed from the stretcher.
To stabilize the silk, cut 1 " wide strips of fusible interfacing [Pellon(TM)950F SirTailor®] and iron-fuse the strips along the edges of the silk. Since this product is wash-fast and dry-cleanable, it will hold up to DyeColour(TM) painting processes and techniques. The stabilized edge also protects the silk from pulls and uneven tension marks created where the silk is attached to the stretcher. In addition, stabilized edges can make it easier to square up a finished painting for framing or if not applicable, the stabilized edge can be removed by simply cutting it off.
When working on rolled hem scarves some fabrics like crepe de chine tend to scallop between the fabric attachment points. You can alleviate the tension by inserting stainless steel quilter's pins along the rolled hem and then place the hooks over them. This technique is very useful because it keeps the grain of the silk straight when executing a straight boarder or geometric design. You can also slip a long slim rod into the roll of the hem and attach the hooks over it or employ charted needles, which are commonly used for smocking.
When working with simple pre-constructed garments that have curves, use long lei needles, which bend to the curves and have memory. Lei needles can be purchased in Hawaii and from some floral supply companies. Cut off the eye of the needle so it does not catch on the threads. To avoid rust stains, do not leave the lei needles in the silk for an extended time.
When painting a scarf with a rolled hem the field dries faster than the wet dye in the rolled hem, which starts to work its way into the drier field causing an uneven watermark. To alleviate the uneven drying, pinch the dye out of the rolled hem with an absorbent paper towel, being careful not to back stain the silk with dye already collected on the towel. As the scarf dries, periodically dry the rolled hem with a hair drier.
New Tip
Manufacture's Diluents (wetting agent)
The diluents I use for DyeColour(TM) painting are the manufactures dye thinners. The dye thinner contains a wetting agent that softens and breaks the surface tension of the fabric helping the dye to penetrate the fabric evenly. Unlike alcohol diluents that dissipate as they dry, the wetting agent remains in the silk. With this in mind, before I start painting, I apply one coat of the manufactures dye thinner to the entire surface of the silk and allow it to dry. Consequently, as I paint, I generally only need to add water to dilute the dye.
Applying Dye Thinner (wetting agent)
To apply the manufactures diluents, follow the directions on the bottle for diluting the concentrate and use a clean wash brush (not a sponge brush) to apply it to the topside of the thoroughly dry latex treated silk. After applying the dye thinner to the silk it can be dried with a hair dryer.
New Tip
Securing Stencils on the Silk
The way you secure a stencil is determine by the effects you want to achieve and intricacy of the stencil design.
Plastic, waxed leaves and waxed Manila stencils can be held in place on stretched silk with small round Crafter's Choice extra strength magnets. But if the suspended silk bounces or the stencil is not tight against the silk, the edges of the image being created may end up a little soft. In some cases the contrast of soft and hard edges maybe desirable.
If a crisp edge is desired, the silk should be stabilized so that it does not bounce and the stencil should be held tight and flat up against the silk. To stabilize and support the silk, cover a piece of foam core with freezer paper (shinny side up) and place the foam core under and up against the silk. Then secure the stencil by placing straight silk pins through the stencil and the stretched silk into the foam core. Once the dye has been applied immediately remove or clean the pins with a cotton swab so the liquid dye does not have a chance to run down the pins onto the silk. When you are finished using the pins and magnets, then rinse in a cup of water and spread out on a paper towel to dry.
When using an airbrush, the stretched silk can be held in a vertical position instead of flat. The Moyer Design(TM) Fabric Stretching System can be set up like an easel to accommodate the silk in a vertical position.
Older Tips
When using decorative acrylic resists (Sennelier Gold, Silver, Black and H.Dupont Resist in a Tube), allow it to dry naturally. To create a more effective resist, BEFORE PAINTING, heat set the resist with an iron by pressing between a press-cloth to set the acrylic resist into the fabric.
Tip
Be careful when you use a lot of black dye next to yellow and colors, which contain a concentration of yellow. Due to the different strike time of the two colors, the black may bleed into the yellow during the steaming process.
Tips on Applicators
To assemble metal tip to plastic applicator: Remove metal tip and pin from inside the bottle. Cut off the plastic tip half way betweeen the top of the tip and the plastic ridge on the tip. Screw the metal tip onto the plastic tip. Once the metal tip is firmly in place, refrain from removing it.
As you are applying the resist the edges of the metal tips may drag slightly on the silk. This is not a terrible problem but you can round off the tip with a jeweler?s file or any fine metal file so that the tip glides easily over the silk. With less resistance you will have more control of your resist drawing and application.
|